カジ旅評判
<ウェブサイト名>
<現在の時刻>
TOP ニュースリリースガイド ニュースリリースガイド一覧 新エネルギー 省エネルギー 材料 Focus NEDO FocusNEDO一覧 Focus NEDO第88号/特集 人とAIが協力し合う未来へ 次のAIが見えてきた Focus NEDO第87号/特集 省エネ・脱炭素への道をひらく 未利用熱エネルギー活用技術 Focus NEDO第86号/特集 AIエッジコンピューティング Focus NEDO第85号/特集 材料開発の革新に三位一体で挑む 超超プロジェクト 第84号/カーボンリサイクル・窒素循環・アンモニア発電・プラスチックリサイクル 資源循環社会への道 第83号/日本の主力エネルギーを目指す 再生可能エネルギー 第82号/イノベーション創出を加速 スタートアップ支援 第81号/実用化へのカウントダウン『セルロースナノファイバー』 第80号/イノベーションで未来をつくる NEDO40年のあゆみ 第79号/ムーンショット型研究開発事業-地球環境の再生へ Cool Earth & Clean Earth 第78号(技術戦略研究センター/スマートセル技術) 第77号(AI・ロボットのNEXTステージ/『オープンイノベーション白書』で読み解くイノベーション創出の今と未来) 実用化ドキュメント 実用化ドキュメント一覧 新エネルギー 省エネルギー 環境問題対策 電子・情報 材料 ロボット・AI・福祉機器 バイオ・医療 NEDO Channel NEDO Channel一覧 新エネルギー 環境問題対策 電子・情報 ロボット・AI・福祉機器 国際 分野横断 その他 NEDO Channel --> 検索 NEDO Channel NEDO公式X NEDO公式Facebook NEDOホームページ トップページ 実用化ドキュメント 世界最高水準の高効率・大型ガスタービンで、地球環境やエネルギー問題に貢献 CONTENTS INTRODUCTION 熱効率61%以上 BEGINNING 大型ガスタービン市場で 世界最高性能を誇る BREAKTHROUGH ガスタービンの要素技術を オールジャパンで開発 FOR THE FUTURE 今後は高温化よりも システム化で高効率化を目指す FACE 大企業の中でもベンチャースピリットを 忘れることなく世界初にチャレンジ なるほど基礎知識 NEDOの役割 メニュー閉じる 省エネルギー 火力発電用高効率ガスタービン開発 世界最高水準の高効率・大型ガスタービンで、地球環境やエネルギー問題に貢献 三菱重工業株式会社 取材:December 2012 INTRODUCTION 概要 熱効率61%以上 2011年3月11日に発生した東日本大震災を機に火力発電への依存度が高まっています。現在、日本の電力需要の約9割が火力発電で賄われています。そうした中、熱効率が60%以上と高く、CO2やNOxなどの排出量が石炭火力などに比べて約50%も少ないことから注目が高まっているのが「ガスタービンコンバインドサイクル発電システム(GTCC)」です。同システムの要となる大型ガスタービンの本格的な開発がわが国で始まったのは1978年度から実施されたナショナルプロジェクト「ムーンライト計画」にさかのぼります。その後も、NEDO主導で実施された「ニューサンシャイン計画」などに引き継がれ、さらなる性能向上が図られてきました。ムーンライト計画当時からプロジェクトに参画してきた三菱重工業では、欧米勢がけん引する大型ガスタービン分野において、世界最高性能の大型ガスタービンを次々に開発。例えば2011年2月から同社高砂製作所の実証プラントで運転開始した「1,600℃級J型ガスタービン」は熱効率61%以上を誇り、ナショナルプロジェクトを通じて開発した高性能フィルム冷却技術を搭載しています。2012年1月~9月の発電用大型ガスタービンの世界シェアはシーメンスが38%に対して三菱重工業は26%と、32%のGEと二位を争うところまで追いついてきました。このような大型ガスタービンは現在の日本の電力需要と地球温暖化防止対策に大きく寄与しているだけでなく、今後、電力需要の大幅な増大が見込まれる新興国においても大きく貢献することが期待されています。 BIGINNING 開発への道 大型ガスタービン市場で世界最高性能を誇る 火力発電の燃料には、主に石炭、石油、天然ガスが使われていますが、その中でも天然ガスは石炭や石油に比べてCO2排出量が大幅に少ないことから、現在、発電電力量の拡大が急速に進んでいる燃料です。そして、天然ガスを燃料とする発電システムのうち、最も熱効率が高いものとして期待が寄せられているのが、「ガスタービンコンバインドサイクル発電システム(GTCC)」です。 GTCCはガスタービンに蒸気タービンを併設した発電システムです。ガスタービンでの発電に加え、その際に生じる高温の排ガスを利用して蒸気タービンも回しダブルで発電しているため、ガスタービンや蒸気タービン単体に比べて10%以上も熱効率が高いのが特徴です(図1)。 図1 ガスタービンコンバインドサイクル(GTCC)の構成 加えて、GTCCは設置も短期間で済み、しかも、安定した電力供給が可能なことから、日本だけでなく今後電力需要の大幅な増大が見込まれる新興国においてもニーズが高まっていくことが予想されます。 GTCCの性能を左右するのが、大型ガスタービンです。大型ガスタービン市場は長年にわたり、欧米のメーカーが席巻してきました。しかし、そうした中にあって、三菱重工業は世界最高性能の大型ガスタービンを次々と開発し、技術力の高さを示してきました。 実際、三菱重工業が開発し、2011年2月から同社高砂製作所の実証プラントで運転を開始した最新の大型ガスタービン「1,600℃級J形」は、電力不足が心配された関西地域の電力需要を賄う大きな支えとなりました。その性能は世界最高レベルの熱効率(61%以上)と電力容量約(46万kW)で、世界各国から注目を集め、発注も相次いでいる状況です。 市場を席巻する欧米勢にナショナルプロジェクトで対抗 ガスタービンの歴史は1930年代にさかのぼります。英国とドイツが航空機用のジェットエンジンを開発したのが始まりです。その後、スイスのBBC(現ABB)社がジェットエンジンを応用してガスタービンを試作し、運転に成功しました。一方、米国でも軍事技術として早くからジェットエンジンの開発に取り組み始めていました。そして1970年代、欧米ではすでに国家戦略として、高効率ガスタービンの開発を推進しており、国際競争力の向上を図っていたのです。 一方、日本でいち早く、ガスタービンの自社開発に取り組み始めたのは、三菱重工業でした。同社は1960年代、米国ウエスティングハウスとの技術提携の下、日本で初めて「700℃級ガスタービン」の製造に成功しました。しかしながら、日本全体としては1970年代に入っても、ガスタービン市場は小さいままで、欧米のメーカーからの輸入に頼っているという状況にありました。 そうした中、1973年と1979年の2度にわたり、オイルショックが日本を襲いました。そこで、日本は石油依存からの脱却と発電システムの高効率化、国際競争力の向上を図るべく、1978年度から10年間にわたり、ナショナルプロジェクトとして、「ムーンライト計画」を実施しました。その中では、高効率ガスタービンの技術研究組合が組織され、三菱重工業をはじめ日立製作所や東芝、川崎重工業など計15の民間企業と国内電力が集結し、ガスタービンに関する技術開発がオールジャパン体制で開始されました。 その間、三菱重工業は同プロジェクトを通して培った要素技術を基に、ガスタービン「1,150℃級D形」を開発しました。そしてこれを主機に、日本で初めて大型GTCCを製造。1984年、東北電力の東新潟火力発電所に設置しました。同GTCCは48.5%という当時、世界最高レベルの熱効率を達成したと同時に、従来の石炭火力発電に比べ約10%の効率向上も果たしました。 その後も三菱重工業は、NEDO主導で実施されたニューサンシャイン計画や、1,700℃級ガスタービンの要素技術開発などのナショナルプロジェクトを通じて、技術力を強化していきました。そして、1989年に実用化した「1,350℃級F形」、1997年に実用化した「1,500℃級G形」、そして最新の「1,600℃級J形」といった具合に、着々と大型ガスタービンの高性能化を実現していったのです。その結果、現在では、欧米勢を上回る高性能な大型ガスタービンを開発するに至り、国内外から高い信頼を得ています(図2)。 図2 三菱重工業が開発したガスタービンとGTCCの性能変遷 現在は三菱総合研究所副理事長で、三菱重工業の元副社長でもあり、ムーンライト計画前から40年にわたってガスタービンの技術開発に携わってきた青木素直さんはこう話します。「1,150℃級や1,600℃級といった名称からも分かるように、ガスタービンの高効率化を図るには、燃焼ガスの温度を上げていくことが不可欠です。それゆえ、ガスタービンの開発の歴史は、燃焼ガスの温度向上に伴う技術開発の歴史だったという言い方ができるでしょう。100℃単位で燃焼温度を上げていくわけですから、その都度、新たな技術開発と既存技術の大幅なバージョンアップが必要で、その取り組みは今なお続いています」 また、1,350℃級F形のガスタービンから開発に携わってきた三菱重工業原動機事業本部ガスタービン技術部次長の伊藤栄作さんはこう説明します。「燃焼ガスの温度とは、具体的にはタービンの入口温度のことを指します。一口に燃焼ガスの温度と言っても1,000℃を超す高温です。そのため、開発すべき技術は多岐にわたり、難易度はどれも最高レベル。とても民間企業1社で乗り越えられるものではありませんでした。欧米各国が国を挙げて企業を支援しているのもそのためです」 燃焼温度を高めることとNOx排出量の低減という二律背反に挑戦 ガスタービンの高効率化には燃焼温度を高めることが必要です。このためには、3つの構成要素である「燃焼器」「タービン」「圧縮機」の全てにおいて、様々な技術開発が必要でした。 通常、天然ガスの燃焼温度が高まれば、NOxの発生量は指数関数的に急増します。しかしながら、NOxの排出量は法令によって厳しく規制されています。そのため、いかにNOxの発生量を抑えて燃焼温度を高めるかが、最初の課題となりました。 三菱重工業はその課題に対して、まず「予混合燃焼」という燃焼方法を考案しました。予混合燃焼とは、あらかじめ天然ガスと空気を混合しておき、燃焼させる方法です。従来は、燃焼器内にある高温高圧の空気の中に天然ガスを吹き込み、燃焼させる「拡散燃焼」という方法が採られていました。 予混合燃焼器(展示品) 拡散燃焼では、燃焼器中の天然ガスの濃度にはどうしてもムラができてします。燃料は、濃度が高すぎても低すぎても燃焼しません。ちょうど良い濃度のところで燃焼します。その結果、拡散燃焼では、局所的に温度の高い場所ができてしまい、そこで大量のNOxが発生してしまいました。 そこで、三菱重工業は世界で初の予混合燃焼の実用化にチャレンジしました。予混合燃焼では、天然ガスと空気を予め均一に混ぜることで、天然ガスの濃度のムラを無くします。これにより、局所的に温度が高くなることが無くなり、NOxの排出量を大幅に減らすことが可能と考えたのです。 しかし、そうすると、燃焼が不安定になってしまいます。そこで、まずは拡散燃焼器と予混合燃焼器を組み合わせたハイブリッド型燃焼器を開発することから始めました。燃焼安定性の高い拡散燃焼器を種火にすることで、予混合燃焼器の不安定性を補う方法です。 この方策は見事に成功しました。1984年、東新潟火力発電所に設置した1,150℃級D形に世界初の予混合燃焼器が導入されました。この取り組みは高く評価され、1985年に国際ガスタービン学会でJ.P.Davis賞を受賞しました。 その後も三菱重工業は予混合燃焼の比率を高めるべく、「マルチノズル」など新たなコンセプトを積極に取り入れ、改良を重ねていきました。その結果、1,150℃級D形では約30%を占めていた拡散燃焼器の燃焼比率が、1,500℃級G形では数%まで低減されました。それに伴い、NOxの排出量も大幅に削減されたのです(図3)。 図3 予混合燃焼器の改良による高温燃焼化とNOx低減の関係図 高温高圧ガスからタービン翼を守る技術で燃焼温度を高める タービンは燃焼器から排出される高温高圧ガスを回転エネルギーに変えます。タービンは数段からなり、回転させるための翼が約500枚も設置されています。翼には、回転して"風車"の役割を担う「動翼」と、回転せず風車を回す際に息を吹きかける"口"の役割を担う「静翼」の2種類があります。 燃焼温度の高温化に伴う最大の課題は、高温高圧ガスによって翼が溶解するのを防ぐことでした。そのため三菱重工業は、「耐熱材料開発技術」「冷却技術」「遮熱コーティング技術」という三つの技術開発に取り組み、順次導入していきました。 1500℃級ガスタービンのローター(手前がタービン) タービン翼は合金でできています。1984年に導入したD形ですら、タービン入口温度は1,150℃にも上ります。そのため、1,000℃を超える温度でも融解しない耐熱合金を開発する必要があり、三菱重工業では耐熱合金開発チームを作り、開発に取り組み始めました。 耐熱合金の融点を上げるには、ニッケルなどベースとなる金属に、コバルトやクロム、モリブデン、タングステン、タンタル、レニウムといったレアメタルを配合することで実現できます。しかしながら、配合の組み合わせは無限大。しかも、配合量の割合を少し変えるだけで、合金の特性は大きく変化してしまいます。 青木さんは、「例えば、タンタルやレニウムの配合量を上げれば、耐熱性能がぐっと高まることはわかっています。しかしながら、タンタルはスマートフォンなどの携帯端末にも不可欠なため、市場動向によって価格が大きく変動します。また、レニウムは非常に希少な金属のため、大変高価です。それゆえ、配合だけでなく、いかにレアメタルの量を減らしつつ耐熱性能を上げるかが最大の課題となりました。現在はコンピューターシミュレーションによって最適な配合を割り出し、さらに実験で確認するという方法で性能向上を図っています」と説明します(図4)。 耐熱合金の開発に加えて、精密鋳造技術の開発も重要でした。GTCC用ガスタービンの翼はジェットエンジンに比べて大型で、しかも、24時間365日、8,000時間以上にわたり高温で連続稼働しなければならないという、極めて過酷な条件が求められます。さらに動翼は毎秒500mの速度で回転しており、大きな遠心力がかかります。このため、翼はクリープの発生が避けられません。クリープとは、物体に持続的に応力が作用することで、時間の経過とともに歪みが増大する現象のことです。 そこで、三菱重工業では、翼の鋳造に当たって、金属の結晶の方向を制御する「一方向凝固翼」を開発しました。これにより、クリープ強度を高めることができました。一方向凝固翼は1,350℃級F形から導入されています(図4)。 図4 タービン入口温度の上昇と翼材料の耐久性向上の推移 耐熱合金の開発により、現在では翼の融点は1,350℃まで向上しています。とはいえ、G形は1,500℃級、最新のJ形は1,600℃級で、そのままではやはり翼は溶けてしまいます。そこで、三菱重工業では耐熱合金の開発と並行して、冷却翼の開発にも取り組んできました。冷却翼とは、空洞にした翼の内部と翼の表面の両方を空気により冷却することで、高温高圧ガスから翼を守るというものです。 D形、F形、G形、J形へと、タービン入口温度の上昇に伴い改良を重ね、冷却方法も高度化していきました。最新の翼には数百個もの穴が空いていて、翼の内部に送り込んだ空気は翼の内部を冷やした後、穴を通って外に出て翼の表面をフィルムのように覆いながら流れていきます。それにより、内側と外側の両面で翼を高熱から保護しようというわけです。青木さんは、「私たちは、この冷却方法を『フィルム冷却』と呼んでいます。最新の1,600℃級J形では、ナショナルプロジェクトを通して開発した高性能フィルム冷却を装備しています」と説明します(図5)。 図5 冷却翼改良の変遷 ブレードの冷却孔 第1段動翼(左)と最後尾(右)ブレードの表面 三菱重工業は、さらに遮熱コーティング技術も開発しました。これは、熱伝導率の低いセラミックスを翼の表面に吹きつけ、コーティングすることで、翼を高熱から守ろうというものです。1986年に実用化した「1,250℃級MF111形」から採用されました。MF111形は、当時の発電用としては世界最高のタービン入口温度を達成しました(図6)。 図6 高温下に対する冷却技術、コーティング技術の関係図 「セラミックスの厚みは0.3mm程度です。あまり厚くし過ぎると、耐熱合金との温度差が原因ではがれやすくなってしまいます。そこで、直径30~150μのセラミックスの微粒子をプラズマで溶かし、翼に均一に薄く吹き付けるための独自技術を開発しました」と青木さん。 また、伊藤さんは、「耐熱材料開発には、長期間にわたる研究とデータ取得が必要です。そのため、今後は冷却技術と遮熱コーティング技術のさらなる向上で、1,700℃級ガスタービンの実現を目指していく計画です」と言います。 世界最高性能の高圧力比圧縮機を開発 ガスタービンを構成する3要素のうち、圧縮機に関しても、様々な技術開発が行われました。ガスタービンの性能を向上させるには、燃焼に使う空気の圧力比を高めることも重要です。圧力比とは、圧縮前と後の空気の圧力比率のことです。圧縮機に取り付けられた翼を使ってより多くの空気を圧縮機内に取り込み圧縮していくことで、圧力比を高めることができます。 701F型ガスタービンの模型(中央部に圧縮機) 従来、三菱重工業を含め、ガスタービンメーカーは、NASA(米国航空宇宙局)の前身で、1915年に設立されたNACA(米国航空諮問委員会)が開発した翼をそのまま採用していました。しかし、三菱重工業では、1997年に実用化した1,500℃級G形開発にあたり、最新のコンピューターシミュレーションを駆使した3次元翼設計技術を適用して、翼を一から設計し直しました。その結果、1,350℃級F形圧縮機に適用された技術では、20段必要なところを17段に縮めることに成功しました。さらに、J形では15段を実現しています。 段数を減らすことのメリットは、ガスタービン全体の長さを短縮し小型化できる点にあります。同じ形状の翼であれば、段数が多いほど圧力比は高まります。ところが、逆にガスタービンの回転軸が長くなるため、振動特性が悪化し、安定した運転ができなくなってしまいます。それゆえ、回転軸の長さには絶対的な制約が課せられているのです。 青木さんは、「制約条件の中で、いかに圧力比を高めるかが、ガスタービンメーカーにとって大きな課題でした。しかしながら、我々はコンピューターシミュレーションを駆使することで、いち早くこの課題に対応したのです」と語ります。 このようにして、三菱重工業は、様々な技術開発を継続的に行っていくことで、ガスタービンの高効率化を図っていったのです。 2011年2〜10月、三菱重工業高砂製作所の実証プラントで試運転が行われた最新のJ型ガスタービンの開放点検結果。各部品の高い信頼性が確認された BREAKTHROUGH プロジェクトの突破口 ガスタービンの要素技術をオールジャパンで開発 1984年、ガスタービン「1,150℃級D形」を主機とする日本初のGTCCを開発した三菱重工業。当時の世界最高レベルの熱効率48.5%を達成しました。その後も、「1,350℃級F形」、「1,500℃級G形」、「1,600℃級J形」と着々と大型ガスタービンの高性能化を実現し、欧米勢が高いシェアを誇るガスタービン市場において、国内外から高い信頼性を勝ち得ています。青木さんは、「三菱重工業が多くの実績を積み重ねることができた要因は、1978年度から実施されたナショナルプロジェクト『ムーンライト計画』なしでは語れない」と言います(図7)。 図7 三菱重工業(MHI)におけるガスタービン開発史とナショナルプロジェクト 「三菱重工業は約50年間にわたり、ガスタービンの開発に取り組んできました。中でも初めて単独で開発した1986年実用化の『MF111』は、その後の開発のベースとなる要素技術の多くを盛り込んだ"原点"とも呼べるガスタービンです。その要素技術は、1978年から10年間、実施されたムーンライト計画を通して培ったものです」(青木さん) これは三菱重工業のみならず、他の日本企業にとっても同様でした。1970年代、欧米が国家戦略として高効率ガスタービンの開発を推進している一方で、日本では、輸入に頼っているという状況にありました。とはいえ、企業が独自に開発するには、大きなリスクと莫大なコストが伴います。そのため、どの企業も最初の一歩を踏み出せずにいました。 一方で、エネルギー資源のほとんどを海外に依存している日本は、世界的なエネルギー需要動向によって社会的、経済的影響を大きく受けます。そういった中で起こった2度のオイルショックは日本に、エネルギー供給システムの安定化やエネルギー転換・利用効率向上の重要性を強く印象付けました。 国力の強化や環境対策、石油代替化など今後のことを考えると、日本も早急に自国でガスタービンを開発できるようにする必要がありました。そこで実施されたのがムーンライト計画でした。 ムーンライト計画では、高効率ガスタービン開発のための技術研究組合が組織され、三菱重工業をはじめ日立製作所や東芝、川崎重工業など計15の民間企業と国内電力が集結しました。そして、総合熱効率50%、出力10万kW、燃焼温度1,300℃の高効率ガスタービンのパイロットプラントの運転研究が、東京電力袖ヶ浦火力発電所構内で実施されました。 その結果、総合熱効率は世界最高の51.7%、出力9.3万kWを実現しました。また、プロトタイププラント用のタービン翼と燃焼器を組み込んだ高温タービン試験装置は世界最高のタービン入口温度1,400℃を達成したのです。 ここでは、耐熱合金、耐熱セラミックスの材料開発、鋳造をはじめ、燃焼器、タービンの翼の冷却方法など、前ページで説明した、ガスタービンを開発する上で不可欠な基幹技術のほぼ全てが開発されました。 「当初は、欧米勢へのキャッチアップという意識が強かったのですが、この成功が私たちを含め、日本企業に、『欧米メーカーに頼らずとも、日本だけで開発できる!』という大きな自信と誇りをもたらしました。その自信と誇りがさらなる開発意欲を掻き立てる大きな原動力になったのです。もしムーンライト計画による国の支援がなければ、日本は今も欧米企業からガスタービンを輸入するだけの立場に甘んじていたことでしょう」と青木さんは言います(図8)。 図8 わが国の従来型火力発電とガスタービンコンバインドサイクル(GTCC)発電の発電効率の変遷 また、機械メーカーだけでなく、素材メーカーや金属メーカーなど技術立国日本を担う様々な分野の企業が参画し、基盤技術の確立と向上を図れたことで、日本の産業全体の大きな底上げにもつながりました。 「多くの企業が集まって一つのものを作るわけですから、もめ事の起きない日はないぐらいでした。しかしながら、ガスタービンは機械工学のあらゆる要素を含んでおり、しかも全てが最先端でなければならないため、技術者にとってこれほど面白い題材はありません。けんかをしながらも同じ技術者同士、一つの目標に向かって切磋琢磨できたことは、私にとって一生の宝となりました」と青木さんは振り返ります。 FOR THE FUTURE 開発のいま、そして未来 今後は高温化よりもシステム化で高効率化を目指す ムーンライト計画終了後も、三菱重工業は、ニューサンシャイン計画や1,700℃級ガスタービンの要素技術開発など多くのナショナルプロジェクトを通じて、GTCCの主機となる大型ガスタービンの開発を進めてきました。 一方、同じくムーンライト計画に参画した企業のうち、日立製作所と東芝は中型ガスタービンを、川崎重工業は小型ガスタービンを志向するなど、ガスタービン市場におけるすみ分けが進み、今日に至っています。 青木さんは、「大型ガスタービンは小型、中型に比べて開発費用も莫大でリスクも高いため、三菱重工業にとっては非常にチャレンジングでした。しかし、投げ出すことなく、ここまで大きな事業に育て上げることができた究極の理由は、ガスタービンが大きな魅力を持っていたからだと思います。」と語ります。 学生時代は航空工学科でジェットエンジンの勉強をしていたという青木さん。そのため、卒業後はジェットエンジンメーカーに就職しようと考えていました。ところがジェットエンジンはすでに大きなビジネスとなっており、しかも欧米企業の独壇場でした。そのため、仮に研究開発に携われたとしても、ごく一部、しかも新たな技術を1から開発するといった経験はできないだろうと考えました。 そこで、当時ビジネスとしては、非常に規模が小さかったものの、機械工学として魅力的なガスタービンに着目しました。ガスタービンであれば、幅広い研究開発ができるのではないかと考えたのです。そして、その考えは見事に的中しました。三菱重工業に入社した時、ガスタービンの要素技術開発は、配属された現在の高砂研究所で行われていました。しかし、研究費も少なく、ガスタービンをやりたい技術者が集まった社内ベンチャー的な組織での活動でした。、そこでガスタービンの要素技術開発がほぼ一から始まったのです。その後、40年の間、高砂研究所と高砂製作所の技術者が一丸となって、ガスタービン技術を世界トップレベルへと進化させました。今日、ガスタービンは三菱重工の中核事業となっています。 図9 三菱重工業のガスタービンの高温・高効率化の変遷 一方、伊藤さんはこう話します。「ガスタービン開発の本拠地である高砂製作所の敷地内には、世界で唯一、研究開発拠点である高砂研究所と、設計・製造拠点である高砂製作所、そして、実証実験を行う実証プラントの3つが揃っていて、フィードバックを迅速にかけることができます。この点も開発を加速させる上で、大変有利に働いたと思います。今後も、世界の電力需要と地球温暖化対策に貢献していきます」 現在は、D形、F形、G形、J形の4種類の大型ガスタービンが、各国の経済事情やエネルギー事情に応じて販売されているという状況です。特に、2011年末に、関西電力の姫路第二発電所に納入し、順調に試運転を続けている1,600℃級J形は、2013年秋に営業開始予定で、試運転の段階から、国内外を問わず注文が相次いでいます。また、50Hz地域向けの後継機も出荷予定です。 今後、三菱重工業は、さらなる高効率化を目指し、1,700℃級の製品を開発していく計画です。また、将来的には、ガスタービンと蒸気タービンを併用した現在のGTCCにさらに燃料電池を組み合わせた「トリプルコンバインドサイクル発電システム」を開発することで、熱効率70%を目指すとともに、石炭をガス化しガスと蒸気で発電する「石炭ガス化複合発電(IGCC)」の早期実用化に向けた技術開発も加速させていく計画です。(2012年12月取材) 三菱重工高砂製作所内にある実証プラント外観(左)、プラント内のガスタービン(右) 開発者の横顔 大企業の中でもベンチャースピリットを忘れることなく世界初にチャレンジ 世界一のガスタービン開発にかけた技術者人生 現在、三菱総合研究所の副理事長で、三菱重工業の元副社長の青木素直さんは、入社以来33年間にわたり高砂研究所と高砂製作所でガスタービンの研究開発と新型機開発を行ってきた工学博士です。ガスタービン事業をここまで大きく育て上げた中心的人物の一人でもあります。 「三菱重工業へはガスタービンの研究開発に携わりたいと思い、入社しました。希望通り、在籍中11基もの設計に携わることができました。入社した際のタービン入口温度は900℃級でしたが、退職する際は、1,600℃級になっていました。今後はさらなる高温化よりも、システム化による高効率化を目指していくことになると思いますが、いずれにせよ、ガスタービンは非常に魅力的な製品であることに変わりありません。一生涯で、世界一もしくは世界初というタイトルを獲得できる機会は中々あるものではありませんが、私はガスタービンのお陰で、何度も味わうことができました。経営者時代も含め40年間にわたり、ガスタービンの開発に携わってこられたことは、私にとって最高の喜びであり、幸せな技術者人生だったと改めて思います」 三菱重工業株式会社青木さん 開発当初からのベンチャースピリットは今も健在 1987年の三菱重工業入社以来、ガスタービンの研究開発一筋できた伊藤さんも青木さん同様、学生時代は、航空工学を専攻していました。しかし、学生時代に青木さんの論文などを読み、自分もガスタービン開発の道へ進もうと決意し、三菱重工業に入社しました。 「大型ガスタービンを自社技術のみですべて開発できるというのは、日本では三菱重工業のみでした。そのため、三菱重工業以外への就職は考えられませんでした。ところが、実際に入社してみると、ガスタービンの研究開発担当者はほんの20名程度と小規模なので、大変驚きました。しかしその分、1人でカバーすべき範囲が幅広く、若手でも計画段階から試運転まで関わらせてもらえたので、大きなやりがいを感じました。その後、事業規模はどんどん大きくなっていきましたが、事業開始当時のベンチャースピリットは今でも健在です。若手もベテランも関係なく、一致団結して開発に取り組むという姿勢や、どんな小さなアイデアにも真剣に耳を傾けて、素晴らしいと思えば採用してくれるという風土は、今後も大切に守り、継承していきたいですね」 三菱重工業株式会社伊藤さん なるほど基礎知識 ガスタービンの要素技術をオールジャパンで開発 そもそもガスタービンとは、天然ガスなどの燃料を燃やして動力を得るエンジンのことです。主に大量の空気を吸い込み圧縮する「圧縮機」、高圧の空気と燃料を燃焼させる「燃焼器」、そして、高温高圧になった燃焼ガスを使って回転する「タービン」の3つで構成されています(図参照)。 図 ガスタービンの構成 タービンの回転力を使って発電機の軸を回転させ、その回転エネルギーを電力に変換することで発電しています。また、タービンの回転力の一部は圧縮機の回転にも使われます。 タービンの回転力を電力として取り出す代わりに、タービンから出る排気エネルギーによって排気自身を加速させ、ジェットとして噴出することで推進力を得ているのが、航空機のジェットエンジンです。 ガスタービンの性能は、「比出力」と「熱効率」の2つで決まります。比出力とは、ガスタービンに流入する空気の単位流量当たりに取り出せる動力のことで、比出力が大きければ大きいほど小型で大出力になります。 一方、熱効率とは、燃料が持つ熱エネルギーから取り出せる動力の割合のことです。具体的には、取り出した動力を燃料が持つ熱エネルギーで割った値になります。同じ出力の機械を動かす場合、熱効率の高いものほど少ない燃料で動かすことができます。 一般に、比出力を大きくするには、タービンの入口温度と取り込む大気温度の比を大きくします。また、熱効率を高めるには、圧縮機での圧力比を高くします。圧力比とは、大気の圧力と圧縮機で圧縮した空気との圧力の比のことです。 それゆえ、ガスタービンの高効率化を図るには、高温化と高圧力比化を行う必要があります。 NEDOの役割 「火力発電用高効率ガスタービン開発」 このプロジェクトがはじまったのは? エネルギー資源のほとんどを海外に依存している日本は、世界的なエネルギー需要動向によって社会的、経済的影響を大きく受けます。特に1970年代に起こった2度のオイルショックはエネルギー供給システムの安定化やエネルギー転換・利用効率向上の重要性を強く印象付けました。そこで、1978年度から実施された「ムーンライト計画」を皮切りに、火力発電の要となる高効率ガスタービンの開発を支援するナショナルプロジェクトが開始されました。 プロジェクトのねらいは? 1970年代、すでに欧米では、国家戦略として高効率ガスタービンの開発を推進しており、国際競争力の向上を図っていました。それに対し日本では、ガスタービンの市場は小さく、米国から輸入しているという状況にありました。しかし、国力の強化や環境対策など今後のことを考えると、日本も早急に、自国でガスタービンを開発できるだけの技術力を獲得する必要がありました。そこで、欧米に負けない高効率ガスタービンを開発すべくナショナルプロジェクトを立ち上げたのです。 NEDOの役割は? ガスタービンの開発には高いリスクと大きな費用が伴うため、一企業だけで取り組むのは困難です。そこで、1978年度から実施された「ムーンライト計画」では、高効率ガスタービンに必要な各種技術の開発が、オールジャパン体制で行われました。その後、さらなる高効率化を目指すべく、1988年度には、NEDOを主体とする「ニューサンシャイン計画」が実施されました。さらに2004年度からは、産官学を挙げた省庁間連携のナショナルプロジェクト「高効率ガスタービン実用化要素技術」も開始されました。これらのナショナルプロジェクトを通してNEDOは、要素技術開発を中心に支援を続けています。 関連プロジェクト ムーンライト計画/高効率ガスタービンの開発(1978年度~1987年度/経産省直轄) ニューサンシャイン計画/WE-NET/CO2回収対応クローズド型高効率ガスタービン技術(1999年度~2001年度) 省エネルギー革新技術開発事業/先導研究/高効率ガスタービン用タービン翼部材の開発(2010年度~2011年度) お読みいただきありがとうございました。ぜひともアンケートにお答えいただき、お読みいただいた感想をお聞かせください。いただいた感想は、今後の連載の参考とさせていただきます。 アンケートに回答する (法人番号 2020005008480) NEDO WebMagazineとは サイト利用について ©New Energy and Industrial Technology Development Organization. All rights reserved. Top -->
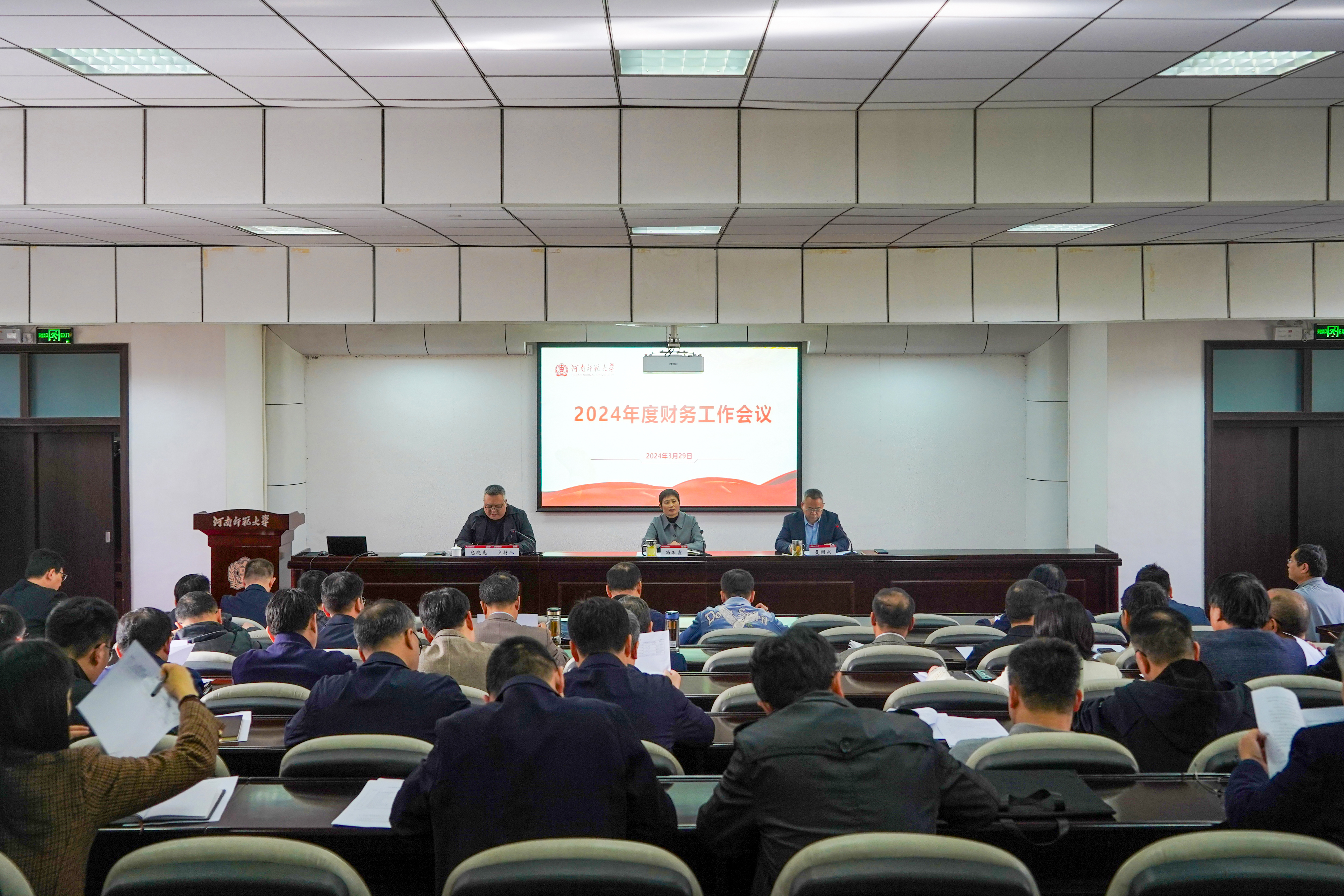